Layout control is a subject with an interesting history and there have been various systems and schemas that have ebbed and flowed in popularity over the years.
When I say layout control, I'm talking about an accessory bus or network and not something whose purpose is to allow you to make your engine move, so let's agree to call those train control for the purposes of these discussions.
Up until this point, most of the layout control systems were an additional use case driven by the need to connect throttles to the DCC command station, but all of these suffer from various architectural deficiencies. The sole exception to the offshoot situation that I can think of is C/MRI - Computer / Model Railroad Interface invented by Dr. Bruce Chubb. C/MRI has been around for a long time and has a pretty solid community around it; in fact many of the CTC systems that I know about use C/MRI as the infrastructure, whether the panel is driven from JMRI or a physical panel.
Various Arduino and other microprocessor based systems have been brewed and used, as model railroader are ingenious in their abilities to adapt things to model railroad use, going back to dyed sawdust as ground cover at the dawn of the hobby.
What these solutions have in common is a single, central problem.
Lack of Sustainability.
They are either the work of a single person (the Arduino schemes are examples) or company (Digitrax, C/MRI, Atlas, Walthers, etc) and in most cases, are closed and proprietary. So once the manufacturer stops making that or goes out of business, you either have to reverse engineer it and potentially run afoul of patents and the like or be willing to run it until it dies and throw it away to start over once you have enough failures that you can't live with it anymore. Similar story if the kids move out and you get that extra space to expand the pike but you can't buy that anymore.
Enter Layout Command Control.
LCC solves the problem, as it is a royalty free and license unencumbered standard that manufacturers are free to implement however they see fit. If a DIY type approach is more to your liking, the standards are available to you so you can work from that angle.
LCC is the adopted standards from the work of the OpenLCB group. OpenLCB was started from what I will call the ashes of the NMRANet project. If one wants to burn a day or three, you can search and find various electrons inconvenienced about NMRANet and how it went a bit pear shaped.
I first saw OpenLCB (still referred to as NMRANet) in 2012 at the Grand Rapids convention. I got an early DevKit, thinking that it would be something somewhat shake and bake. I was so so wrong.
Thankfully, that was then and this is now.
At this point, commercial hardware is available from RR-Cirkits and there are various open source DIY stuff too. I have a mix of RR-Cirkits and the Nucleo DevKit here on the layout. I personally laid out an expansion board for the Nucleo DevKit.
If you check out the main
openlcb.org website you can see the general status. There is even a print book out about LCC!
I will put up more posts as I have time and inclination - this post has sat in a draft status for almost 2 years; its original post date was October 2018...
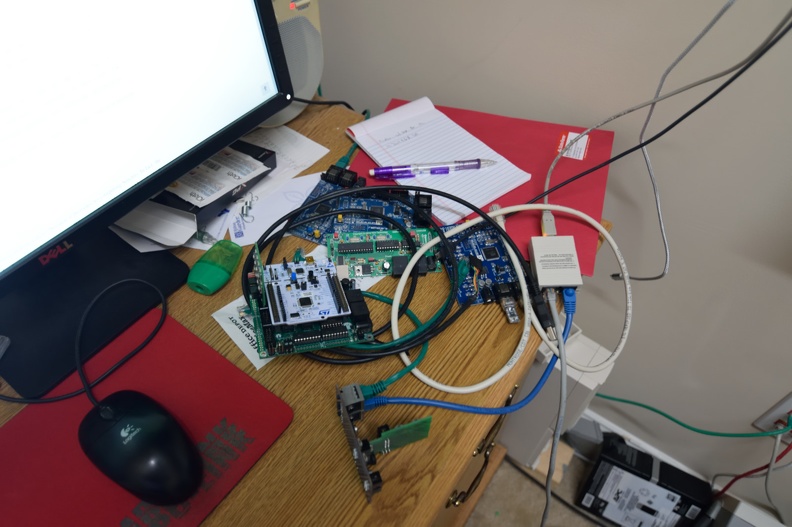 |
From 6 o'clock clockwise: (on edge) RR-Cirkits Tower-LCC, Nucleo DevKit (green and white PCB combo), Railstars IO (Blue PCB), LCC-Buffer. At center is a TCH Technology USB-Serial to CAN adapter that ended up having a fairly serious hardware bug.. |